Unveiling the Wide-Ranging Applications of Laser Welding Technology
Discover how laser welding technology is revolutionizing the manufacturing landscape with its remarkable precision and diverse capabilities.
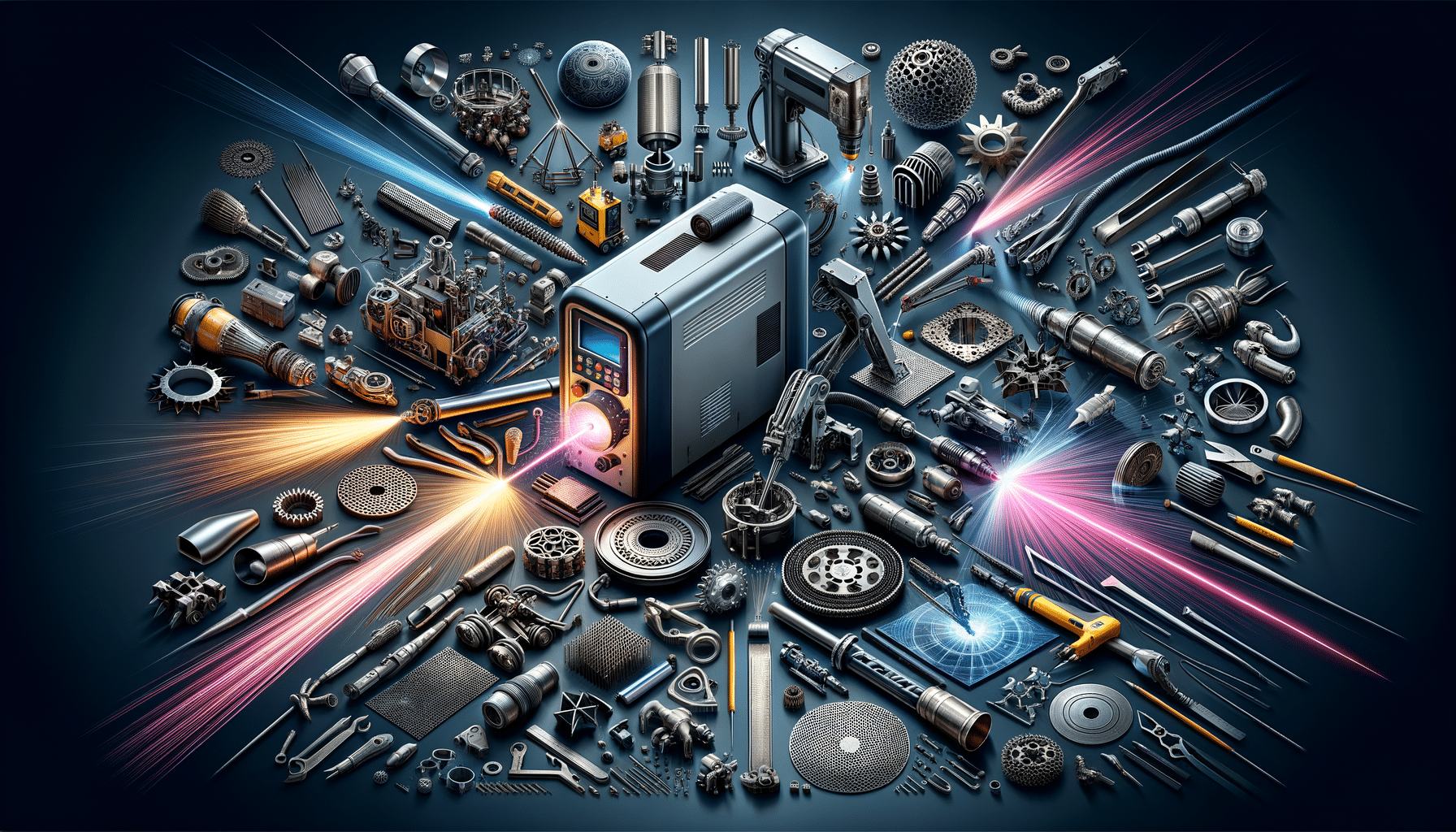
The Evolution and Fundamentals of Laser Welding Technology
Laser welding technology has evolved significantly since its inception, transforming from a niche process into a pivotal tool in modern manufacturing. At its core, laser welding utilizes a concentrated beam of light to join materials, offering precision and control that traditional methods struggle to match. The journey began in the 1960s, with the first practical applications appearing in industries requiring intricate and delicate work, such as aerospace and electronics.
Unlike conventional welding, which often involves direct contact and pressure, laser welding operates in a non-contact manner. This means that the laser beam can be finely focused, allowing for deep penetration and minimal distortion, even in challenging materials. This precision is enhanced by the ability to control the laser’s intensity, duration, and focus, making it suitable for a wide range of applications.
Key advantages of laser welding include:
- High precision and minimal heat-affected zones
- Capability to weld dissimilar materials
- Reduced need for post-processing
- Automation compatibility
These attributes have made laser welding a preferred choice in industries where accuracy and efficiency are paramount. As technology advances, the capabilities of laser welding continue to expand, opening new possibilities for its application.
Applications Across Diverse Industries
Laser welding technology has found its place in a variety of industries, each leveraging its unique benefits to improve production processes. In the automotive sector, laser welding is instrumental in creating lightweight yet strong components, contributing to fuel efficiency and safety. The precision of laser welding allows for the joining of complex geometries and the use of advanced materials such as high-strength steels and aluminum alloys.
In the electronics industry, the miniaturization of components demands a welding process that can handle small, intricate parts without causing damage. Laser welding provides the necessary precision and control, ensuring reliable connections in devices where space and tolerance are limited. This is particularly evident in the production of microelectronics and semiconductor devices.
Another significant application is in the medical field, where laser welding is used to create intricate and sterile components for medical devices. The non-contact nature of laser welding ensures that the materials remain uncontaminated, a critical requirement for medical applications. Furthermore, the ability to weld dissimilar materials is advantageous in creating complex assemblies that incorporate various metals and plastics.
The versatility of laser welding extends to sectors like aerospace, jewelry manufacturing, and even art restoration, showcasing its adaptability and wide-ranging impact.
Comparing Laser Welding with Traditional Methods
When considering welding options, it’s essential to compare laser welding with traditional methods such as arc welding, MIG, and TIG. Each method has its strengths and limitations, and the choice often depends on the specific requirements of the task at hand.
Traditional welding methods like MIG and TIG rely on direct contact and the application of filler materials. These processes are well-suited for heavy-duty applications and can be cost-effective for large-scale projects. However, they often result in larger heat-affected zones, which can lead to warping and require additional post-processing to achieve the desired finish.
In contrast, laser welding offers several advantages:
- Precision: Laser welding provides a higher degree of precision, allowing for cleaner welds with minimal distortion.
- Speed: The process is typically faster, reducing production time and costs.
- Flexibility: The ability to weld dissimilar materials and complex geometries without filler materials.
While laser welding may require a higher initial investment in equipment, the long-term benefits in terms of efficiency, quality, and versatility often justify the cost. As industries continue to demand higher standards of production, the appeal of laser welding technology is likely to increase.
Challenges and Innovations in Laser Welding
Despite its many benefits, laser welding technology is not without challenges. One of the primary concerns is the initial cost of equipment and the need for skilled operators to manage the process. The precision of laser welding requires careful calibration and control, which can be a barrier for smaller operations or those new to the technology.
Material reflectivity is another challenge, as highly reflective materials can cause issues with laser absorption, leading to inconsistent welds. Innovations in laser technology, such as the development of fiber lasers and diode lasers, are addressing these issues by improving beam quality and energy efficiency.
Moreover, advancements in automation and robotics are enhancing the capabilities of laser welding systems. Automated laser welding setups can achieve higher consistency and speed, reducing human error and increasing throughput. The integration of artificial intelligence and machine learning is also paving the way for smarter welding systems that can adapt to varying conditions and optimize performance in real-time.
These innovations are crucial for maintaining the competitive edge of laser welding technology, ensuring it remains a viable and attractive option for industries seeking to enhance their manufacturing processes.
The Future of Laser Welding Technology
As we look to the future, laser welding technology is poised to become even more integral to manufacturing. With continuous advancements in laser sources, control systems, and automation, the scope of applications is expanding. Emerging fields such as additive manufacturing and 3D printing are beginning to incorporate laser welding techniques, further blurring the lines between traditional and modern manufacturing processes.
Environmental considerations are also driving innovation, with laser welding offering a more sustainable alternative to some traditional methods. The reduced need for consumables and lower energy consumption contribute to a smaller carbon footprint, aligning with global efforts to enhance sustainability in industrial practices.
The potential for laser welding technology to revolutionize industries is immense, as it continues to adapt and evolve. From enhancing the quality and efficiency of production to enabling new design possibilities, laser welding is at the forefront of technological innovation.
For manufacturers and engineers, staying informed about the latest developments in laser welding is crucial. Embracing this technology can lead to significant competitive advantages, fostering growth and innovation in an ever-changing industrial landscape.