High-Performance Sandwich Panels for Construction Projects
Sandwich panels are crucial components in modern construction, offering a blend of strength, insulation, and versatility.
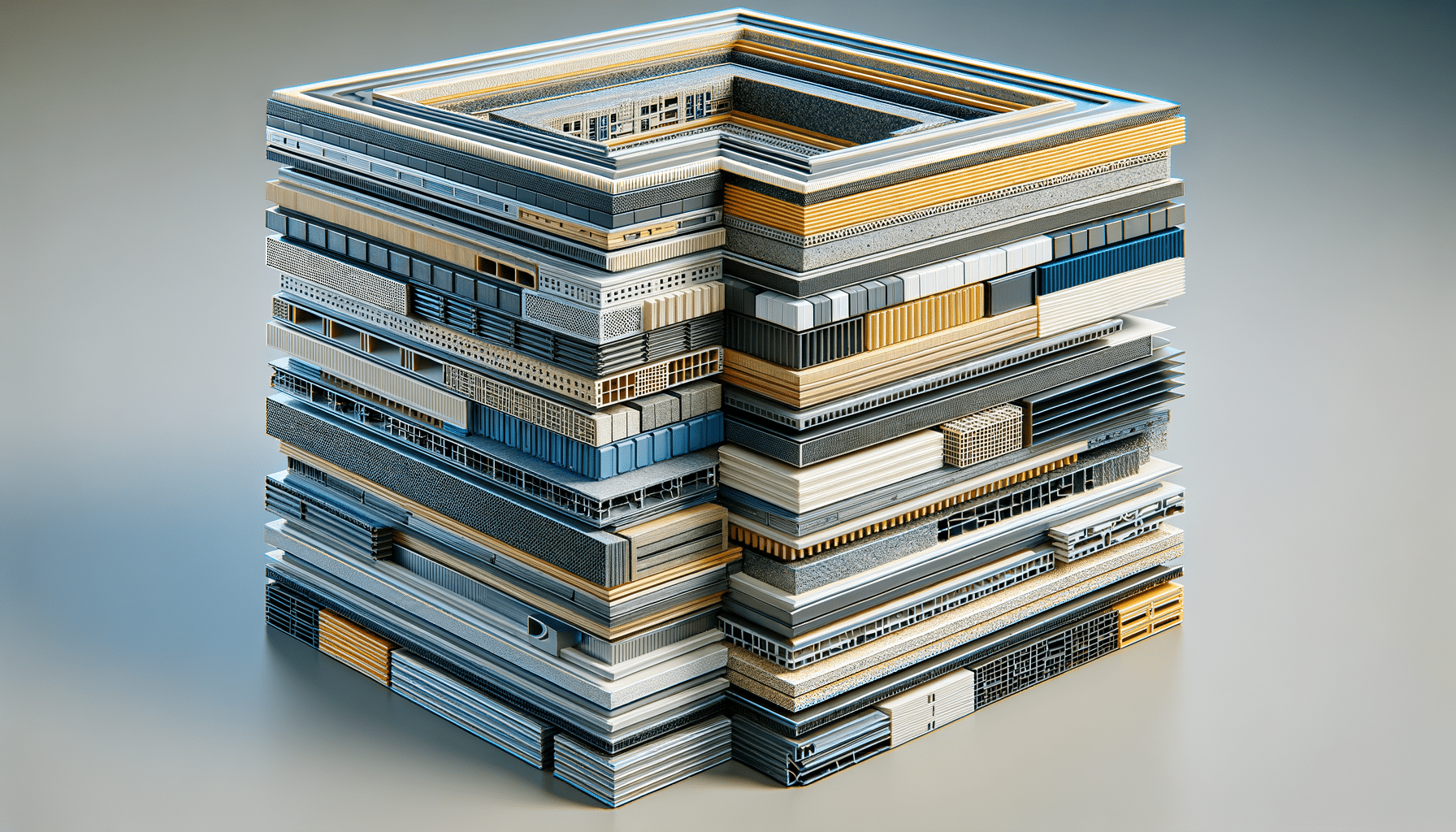
Introduction to Sandwich Panels
Sandwich panels are essential components in modern construction, offering a unique combination of strength, insulation, and versatility. These panels consist of three layers: a low-density core and two thin, rigid outer layers. This structure provides excellent thermal insulation and mechanical strength, making them ideal for a wide range of applications, from industrial buildings to residential homes. The growing demand for energy-efficient and sustainable building materials has further increased the relevance of sandwich panels in today’s construction industry.
Composition and Types of Sandwich Panels
Sandwich panels are composed of three main layers: the core, and the two outer skins. The core material is typically low-density and provides thermal insulation and sound absorption. Common core materials include polyurethane, polystyrene, and mineral wool. The outer skins are usually made from materials like galvanized steel, aluminum, or fiber-reinforced plastics, providing durability and weather resistance.
There are various types of sandwich panels, each suited for specific applications:
- Polyurethane Panels: Known for their excellent thermal insulation properties, making them ideal for cold storage and refrigerated buildings.
- Polystyrene Panels: Lightweight and cost-effective, suitable for general construction purposes.
- Mineral Wool Panels: Offer superior fire resistance and sound insulation, commonly used in industrial and commercial buildings.
Advantages of Using Sandwich Panels
Sandwich panels offer several advantages that make them a popular choice in the construction industry. These benefits include:
- Thermal Insulation: The core material provides exceptional insulation, reducing energy consumption and maintaining comfortable indoor temperatures.
- Lightweight: Despite their strength, sandwich panels are lightweight, reducing the load on building structures and simplifying installation.
- Durability: The outer skins protect against weather elements, corrosion, and mechanical damage, ensuring a long lifespan.
- Cost-Effectiveness: Quick installation and reduced labor costs make sandwich panels a cost-effective solution for many projects.
Applications of Sandwich Panels
Sandwich panels are versatile and can be used in a wide range of applications, from industrial to residential buildings. Some common applications include:
- Industrial Buildings: Used in factories, warehouses, and cold storage facilities for their insulation and durability.
- Commercial Buildings: Ideal for shopping malls, office spaces, and exhibition centers due to their aesthetic appeal and energy efficiency.
- Residential Homes: Increasingly used in modern homes for roofing and wall cladding, providing thermal comfort and reducing energy bills.
Future Trends and Innovations
The demand for sandwich panels is expected to grow as the construction industry continues to prioritize energy efficiency and sustainability. Innovations in materials and manufacturing processes are likely to enhance the performance of sandwich panels further. For example, the development of bio-based core materials and advanced coatings for outer skins could improve environmental impact and durability.
Additionally, the integration of smart technologies, such as sensors for monitoring structural health and energy usage, could revolutionize the use of sandwich panels in construction. As these innovations continue to evolve, sandwich panels will remain a critical component in building the sustainable structures of the future.