The Rising Popularity of Laser Welding: An Overview
Laser welding, with its remarkable precision and efficiency, is reshaping the landscape of various industries.
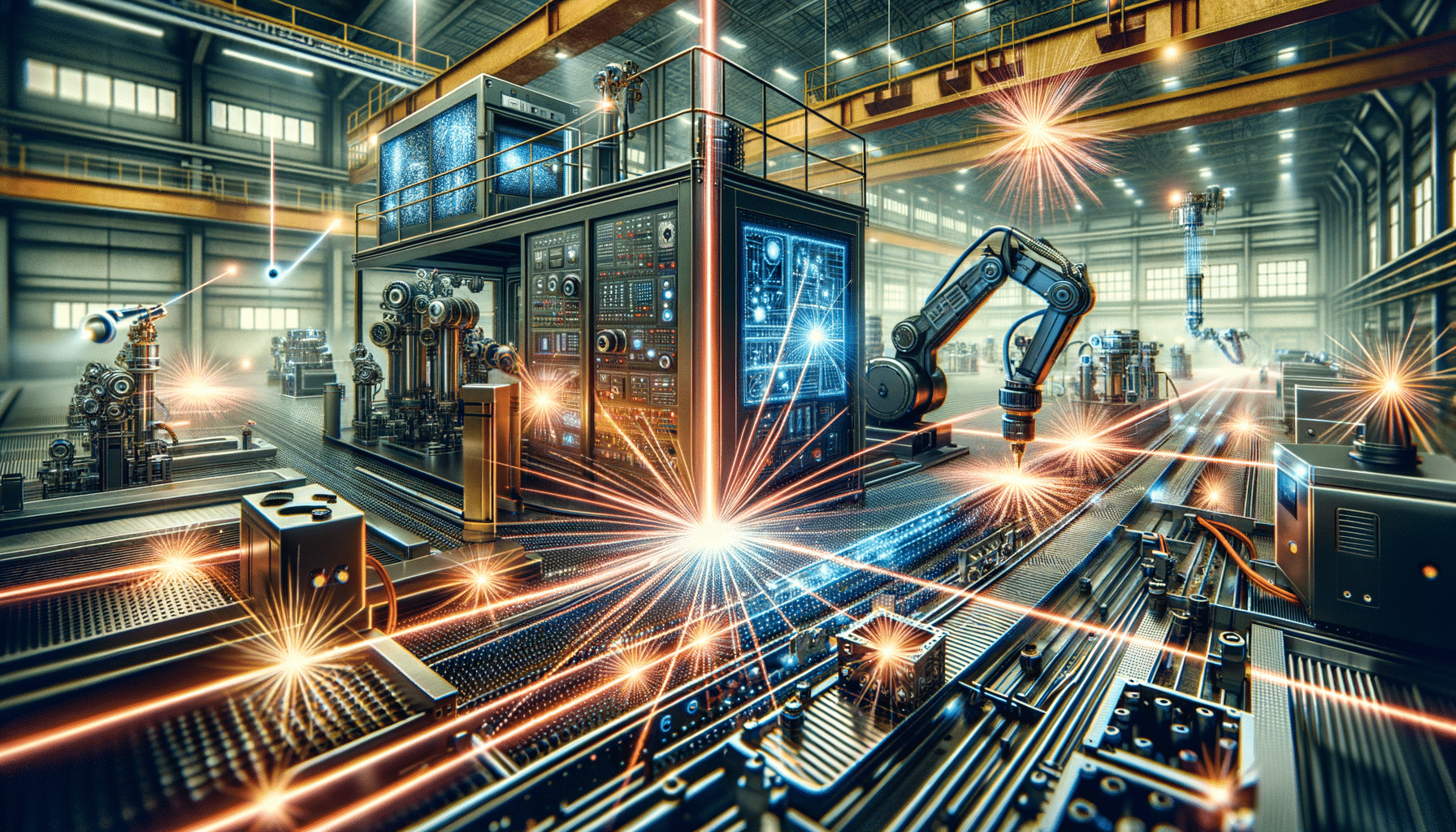
The Precision and Efficiency of Laser Welding
Laser welding has emerged as a pivotal technology in modern manufacturing, celebrated for its precision and efficiency. Unlike traditional welding methods, laser welding uses a focused beam of light to join materials, resulting in a highly concentrated heat source that allows for precise control. This precision is particularly beneficial in industries where intricate and delicate work is required, such as in the electronics and medical device sectors.
One of the key advantages of laser welding is its ability to produce high-quality welds with minimal distortion. The concentrated heat source means that the material surrounding the weld is less affected, reducing the risk of warping or damage. This is crucial in applications where maintaining the integrity of the surrounding material is essential.
Moreover, laser welding is known for its speed. The process can be completed much faster than traditional methods, which not only increases productivity but also reduces costs. The efficiency of laser welding is further enhanced by its adaptability to automation, allowing for integration into robotic systems that can operate continuously with minimal human intervention.
In summary, the precision and efficiency of laser welding make it a highly valued technique in industries that demand high standards and quick turnaround times. Its ability to deliver consistent results with reduced material distortion and its compatibility with automated systems underscore its growing significance in modern manufacturing.
Applications Across Diverse Industries
Laser welding’s versatility is evident in its wide range of applications across various industries. In the automotive industry, laser welding is employed to join components with high precision, contributing to the production of lightweight and fuel-efficient vehicles. The ability to weld dissimilar materials, such as aluminum and steel, is particularly advantageous in automotive manufacturing, where weight reduction is a critical factor.
In the aerospace sector, the demand for lightweight yet strong materials makes laser welding an ideal choice. The technique’s precision ensures that the structural integrity of components is maintained, which is essential for safety and performance in aerospace applications. Additionally, laser welding’s ability to create complex geometries is beneficial in the production of intricate aerospace components.
The medical device industry also greatly benefits from laser welding. The technique’s precision is crucial in the fabrication of medical instruments and implants, where even the smallest imperfections can have significant consequences. Laser welding allows for the creation of small, precise welds that meet the stringent standards required in the medical field.
Overall, laser welding’s adaptability to different materials and its capacity to produce high-quality welds make it a valuable asset across a multitude of industries, each benefiting from its unique capabilities.
Technological Advancements in Laser Welding
As technology continues to advance, so too does the field of laser welding. Recent innovations have expanded the capabilities of laser welding systems, making them more efficient and versatile. One such advancement is the development of fiber lasers, which offer higher power and improved beam quality compared to traditional CO2 lasers.
Fiber lasers are known for their ability to produce a finer, more focused beam, which enhances precision and reduces heat-affected zones. This makes them particularly useful in applications where detailed work is required, such as in the electronics industry. Additionally, fiber lasers have a longer lifespan and require less maintenance, making them a cost-effective option for manufacturers.
Another notable advancement is the integration of real-time monitoring systems in laser welding processes. These systems use sensors and cameras to monitor the welding process, ensuring that any deviations from the desired parameters are detected and corrected immediately. This not only improves the quality of the welds but also reduces waste and increases overall efficiency.
Furthermore, advancements in automation have allowed for the development of fully automated laser welding systems. These systems can operate continuously with minimal human intervention, increasing productivity and reducing labor costs. The combination of these technological advancements has solidified laser welding’s position as a leading technique in modern manufacturing.
Challenges and Considerations in Laser Welding
While laser welding offers numerous advantages, there are also challenges and considerations that must be addressed. One of the primary challenges is the initial cost of laser welding equipment, which can be significantly higher than that of traditional welding systems. However, the long-term benefits of increased efficiency and reduced material waste often outweigh the initial investment.
Another consideration is the need for skilled operators. Although laser welding systems are increasingly automated, the setup and maintenance of these systems require specialized knowledge. Training programs and certifications are essential to ensure that operators are equipped with the necessary skills to manage and troubleshoot laser welding systems effectively.
Material compatibility is also a critical factor in laser welding. While the technique is versatile, not all materials are suitable for laser welding. Factors such as reflectivity and thermal conductivity can affect the quality of the welds. Therefore, thorough testing and material selection are crucial to achieving optimal results.
Despite these challenges, the benefits of laser welding continue to drive its adoption across industries. By addressing these considerations, manufacturers can harness the full potential of laser welding to enhance their production processes.
The Future of Laser Welding
The future of laser welding looks promising, with ongoing research and development poised to further enhance its capabilities. As industries continue to demand more efficient and precise manufacturing techniques, laser welding is expected to play an increasingly vital role.
One area of potential growth is the development of hybrid welding techniques that combine laser welding with other methods, such as arc welding. These hybrid techniques can offer the benefits of both methods, providing improved weld quality and increased productivity.
Another exciting prospect is the integration of artificial intelligence and machine learning into laser welding systems. These technologies can optimize welding parameters in real time, leading to even greater efficiency and precision. The ability to predict and prevent potential issues before they occur could revolutionize the manufacturing process.
As industries continue to evolve, the adaptability and efficiency of laser welding will ensure its place as a cornerstone of modern manufacturing. Its ability to meet the demands of diverse industries and its potential for future advancements make it a technology worth watching.