Unravel the Potential of Modern Welding Machines: A Comprehensive Guide
Diving into the world of welding machines, we explore the variety and precision that these tools bring to the table. From MIG and TIG welders to intricate laser models, we take a journey to understand these modern marvels. Whether you are a seasoned professional or a passionate hobbyist, this guide is designed to help you navigate through the latest welding innovations and discover the perfect tool for your projects.
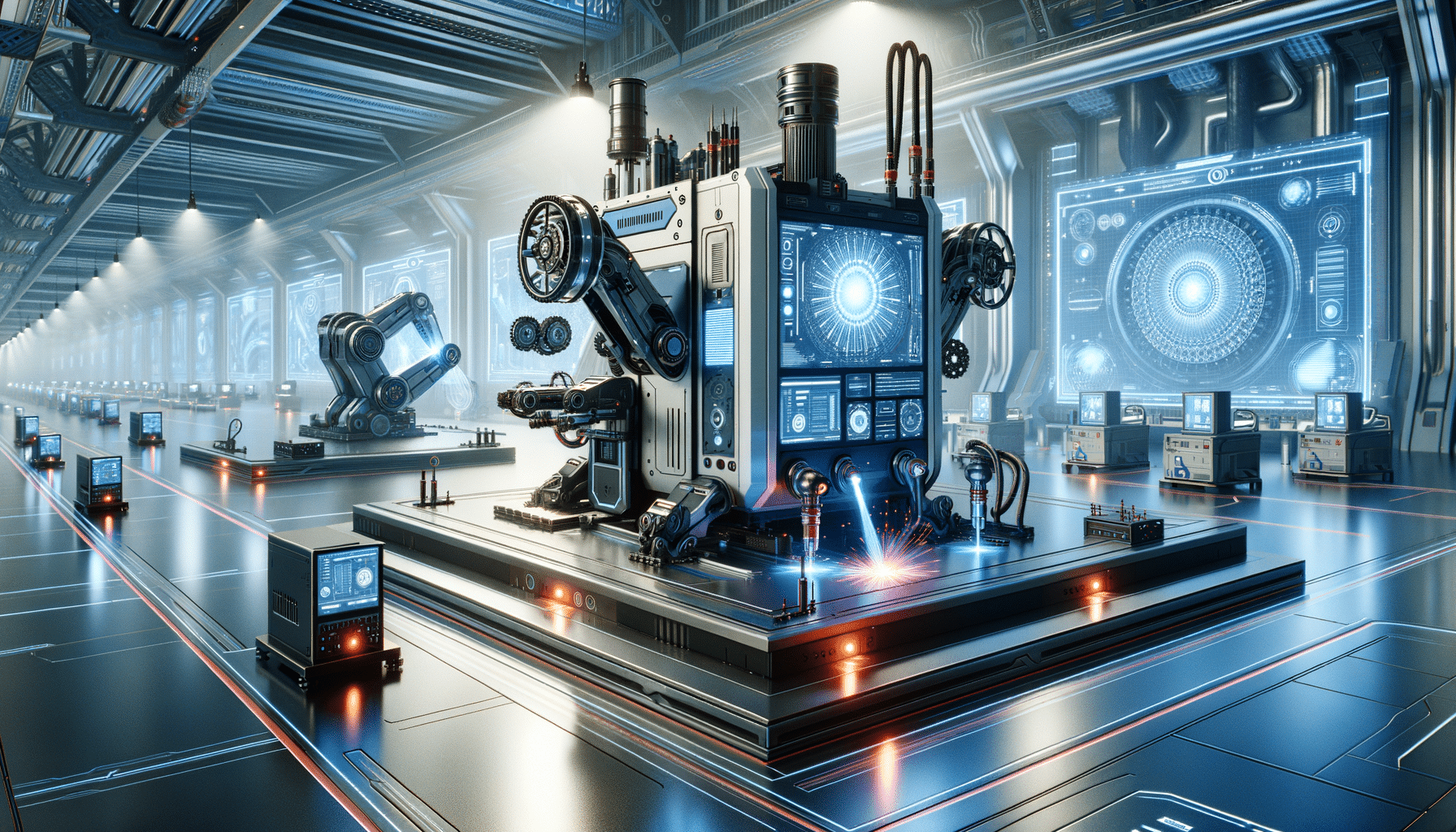
The Evolution of Welding Machines: From Basic to Advanced
Welding has long been a cornerstone of industrial and creative fabrication, evolving significantly from its rudimentary beginnings. The journey from basic stick welding to the advanced machines of today is a testament to technological innovation. Early welding methods were limited in scope and precision, often resulting in inconsistent results. However, with the advent of modern technology, welding machines have become more sophisticated, offering greater control and versatility.
Today’s advanced welding machines are equipped with features that allow for precise control over the welding process. These machines are designed to handle a variety of materials, from traditional metals like steel and aluminum to newer composites and alloys. As a result, they are suitable for a wide range of applications, from automotive manufacturing to intricate artistic projects.
Moreover, the integration of digital technology into welding machines has enhanced their functionality. For instance, many modern machines come with programmable settings that allow users to save and recall specific welding parameters. This feature not only improves efficiency but also ensures consistency across different projects. The evolution of welding machines reflects a broader trend towards automation and precision in manufacturing, highlighting the industry’s commitment to quality and innovation.
Types of Advanced Welding Machines: A Diverse Landscape
The world of advanced welding machines is as diverse as the applications they serve. Each type of machine offers unique capabilities, catering to specific needs and preferences. Let’s explore some of the prominent types.
MIG (Metal Inert Gas) welders are among the most popular due to their ease of use and versatility. They are ideal for beginners and professionals alike, capable of handling a variety of materials and thicknesses. MIG welders are particularly well-regarded for their speed and efficiency, making them a staple in many workshops.
TIG (Tungsten Inert Gas) welders, on the other hand, are known for their precision and control. They are often used in applications where aesthetics and detail are paramount, such as in the aerospace and automotive industries. TIG welding is a slower process but offers superior quality and finish, making it a preferred choice for high-end projects.
Laser welding machines represent the cutting edge of welding technology. These machines utilize concentrated laser beams to achieve high precision and minimal heat distortion. Laser welding is especially beneficial for delicate and intricate work, such as in the electronics and medical device industries. The ability to weld small components with minimal impact on surrounding areas sets laser welders apart from traditional methods.
Each type of welding machine brings its own set of advantages, allowing users to select the one that best fits their project requirements. This diversity ensures that there is a suitable welding solution for every challenge, whether it involves speed, precision, or material compatibility.
Technological Innovations Driving the Future of Welding
As we look towards the future, technological innovations continue to shape the landscape of welding. One of the most significant advancements is the integration of artificial intelligence (AI) and machine learning into welding processes. These technologies enable machines to learn from previous welds, optimizing parameters for improved performance and efficiency. AI-driven welding machines can adapt to changing conditions, ensuring consistent quality across different environments.
Another promising development is the use of augmented reality (AR) in welding training and operations. AR technology provides welders with real-time feedback and guidance, enhancing their skills and reducing the likelihood of errors. This technology is particularly valuable in training new welders, offering a safe and controlled environment to practice and refine their techniques.
Additionally, the rise of collaborative robots, or cobots, is transforming the way welding tasks are performed. Cobots work alongside human operators, taking on repetitive or hazardous tasks while allowing welders to focus on more complex aspects of the job. This collaboration not only improves productivity but also enhances safety in the workplace.
These technological innovations are driving the welding industry towards a future where machines and humans work in harmony. The potential for increased efficiency, precision, and safety is vast, promising exciting developments for both seasoned professionals and newcomers to the field.
Choosing the Right Welding Machine: Factors to Consider
Selecting the right welding machine can be a daunting task, given the wide array of options available. However, by considering a few key factors, you can make an informed decision that meets your specific needs.
First and foremost, consider the materials you will be working with. Different welding machines are designed to handle specific materials, so it’s essential to choose one that aligns with your project requirements. For instance, if you frequently work with thin metals or require high precision, a TIG welder might be the most suitable choice.
Next, assess the power requirements and capabilities of the machine. Ensure that the machine’s power output matches the thickness and type of materials you plan to weld. Additionally, consider the machine’s duty cycle, which indicates how long it can operate continuously before needing a break. A higher duty cycle is beneficial for extended projects or industrial applications.
Portability and ease of use are also crucial factors, particularly if you need to transport the machine between job sites. Lightweight and compact models are ideal for mobile operations, while larger machines may offer more features and power for stationary use.
Lastly, consider the level of support and training available for the machine. Manufacturers often provide resources such as user manuals, online tutorials, and customer support to assist with setup and operation. Access to these resources can significantly enhance your experience and ensure you get the most out of your investment.
By carefully evaluating these factors, you can select a welding machine that not only meets your current needs but also accommodates future projects as your skills and requirements evolve.
The Impact of Advanced Welding Machines on Industry and Art
Advanced welding machines are making a significant impact across various industries, from manufacturing to art. Their ability to deliver precision, efficiency, and versatility is transforming traditional practices and opening new possibilities.
In the manufacturing sector, advanced welding machines are enhancing production capabilities. They enable manufacturers to produce complex components with high accuracy, reducing waste and improving quality. This precision is particularly valuable in industries such as automotive and aerospace, where even minor deviations can have significant consequences.
Beyond industrial applications, welding machines are also influencing the world of art. Artists are using these machines to create intricate sculptures and installations, pushing the boundaries of what is possible. The precision and control offered by modern welding technology allow artists to experiment with new forms and materials, leading to innovative and captivating works.
Furthermore, the accessibility of advanced welding machines is democratizing the art form, allowing more individuals to explore their creative potential. Hobbyists and DIY enthusiasts can now access professional-grade tools, enabling them to bring their artistic visions to life.
The impact of advanced welding machines is evident in both industry and art, highlighting their versatility and potential. As technology continues to evolve, these machines will play an increasingly vital role in shaping the future of fabrication and creativity.