Unraveling the World of Welding: From MIG and TIG to Laser, and Identifying Top-rated Welding Solutions in Your Vicinity
Understand the importance of choosing the right welding service or machine that aligns with your needs. This guide provides an overview of various welding types – MIG, TIG, laser, and underwater, and gives you insights into welding costs, aluminum and plastic welding techniques. Discover some of the highly regarded welding services and solutions within your locality that match your requirements and economic considerations.
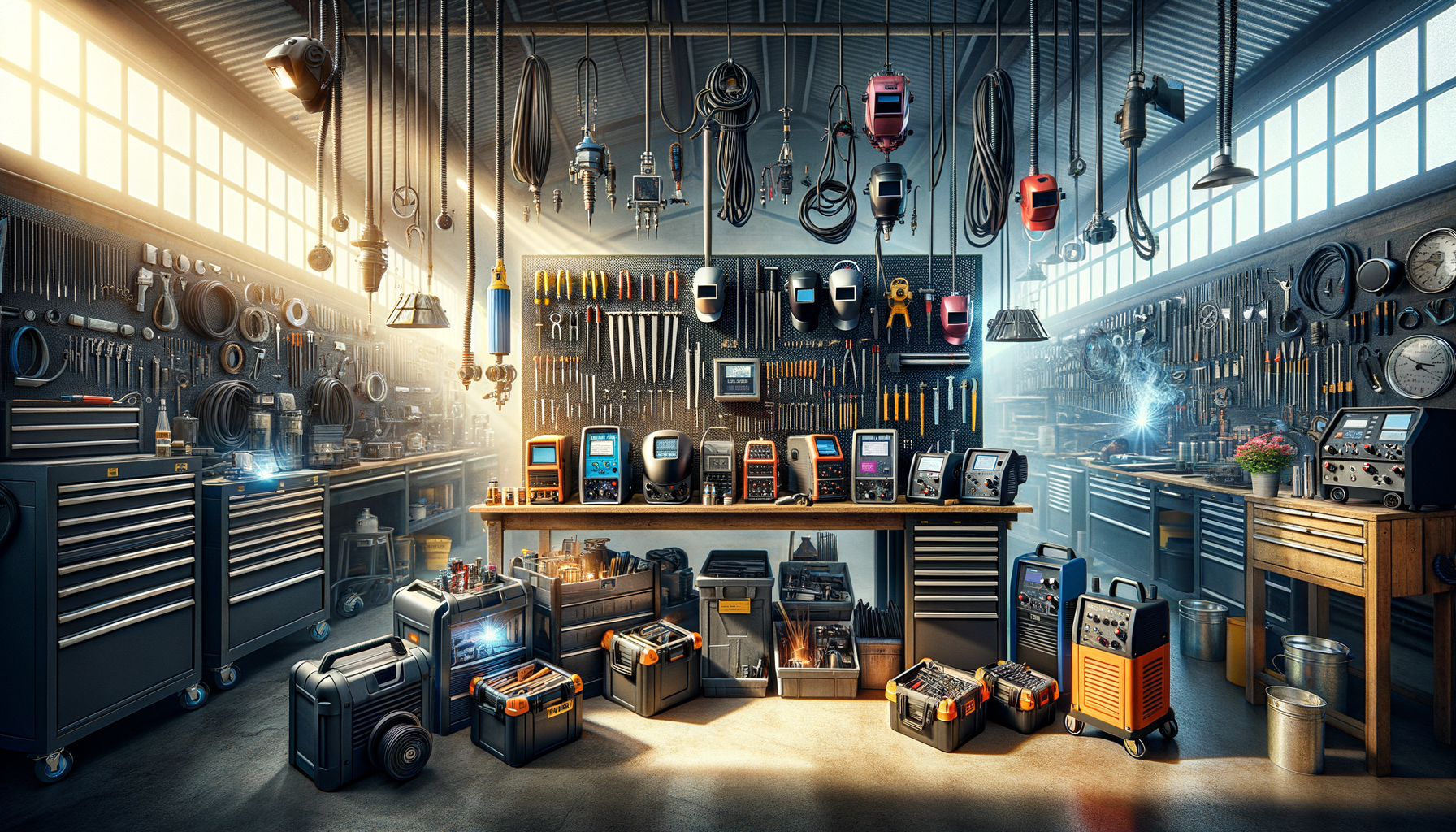
Understanding MIG and TIG Welding Techniques
Metal Inert Gas (MIG) and Tungsten Inert Gas (TIG) are two widely used welding techniques, each with unique applications and benefits. MIG welding is known for its speed and efficiency, making it suitable for large-scale projects. It involves feeding a continuous solid wire electrode through a welding gun into the weld pool, joining the base metals together. This technique is particularly effective for welding thicker materials and is often used in automotive and construction industries.
On the other hand, TIG welding is renowned for its precision and control, which is perfect for thinner materials and intricate work. Unlike MIG, TIG uses a non-consumable tungsten electrode and requires a filler material to create the weld. This method is highly regarded in industries that demand high-quality finishes, such as aerospace and art sculpture. Both techniques have their place, and choosing between them depends on the specific requirements of your project, including material type, thickness, and desired finish.
The Rise of Laser Welding Technology
Laser welding is a cutting-edge technique that has gained popularity in industries requiring precision and minimal thermal distortion. It uses a high-intensity laser beam to melt the materials being joined, resulting in a strong and clean weld. This method is particularly advantageous in the electronics and medical device industries, where precision and cleanliness are paramount.
One of the key benefits of laser welding is its ability to join dissimilar materials, which is often challenging with traditional welding methods. Additionally, the speed and automation potential of laser welding can significantly reduce production times and costs. However, the initial investment for laser welding equipment is higher, which might be a consideration for smaller businesses. As technology advances, laser welding continues to evolve, offering new possibilities for innovation in manufacturing processes.
Exploring Underwater Welding: Challenges and Applications
Underwater welding is a specialized field that combines the skills of a welder and a diver. It is used primarily in the maintenance and repair of ships, oil rigs, and pipelines submerged under water. There are two main types of underwater welding: wet welding, where the welding is directly exposed to water, and dry welding, which involves creating a dry environment around the weld area using a hyperbaric chamber.
While underwater welding offers unique opportunities, it also presents significant challenges. The harsh environment, pressure changes, and risk of electric shock require specialized training and equipment. Despite these challenges, underwater welding remains a vital technique for maintaining marine infrastructure, ensuring the safety and functionality of essential underwater structures. It is a field that demands not only technical expertise but also a high degree of physical fitness and adaptability.
Cost Considerations in Welding Services
The cost of welding services can vary widely based on several factors, including the type of welding, the materials used, and the complexity of the project. For instance, MIG welding might be more cost-effective for large projects due to its speed, while TIG welding, with its precision, might incur higher costs due to the time and skill required.
When considering welding services, it’s important to factor in not just the immediate costs but also the long-term value. High-quality welding can enhance the durability and performance of the final product, potentially saving costs on repairs and replacements in the future. Additionally, some welding services offer package deals or discounts for bulk projects, which can be a cost-effective option for businesses with ongoing welding needs.
To ensure you’re getting value for your money, it’s advisable to compare quotes from multiple service providers and consider their reputation, experience, and customer feedback. Investing in a reliable welding service can ultimately lead to better outcomes and satisfaction.
Finding Reliable Welding Services in Your Area
Locating a reliable welding service in your area involves more than just a quick internet search. It’s crucial to assess the quality and reliability of potential service providers. Start by seeking recommendations from industry peers or reading online reviews. Look for services that have a proven track record and a portfolio of past projects that demonstrate their expertise.
Another important aspect is to verify the certifications and qualifications of the welders. Certified professionals are more likely to adhere to industry standards and deliver quality results. Additionally, consider visiting the workshop to observe their equipment and safety practices. A well-maintained workshop often reflects a commitment to quality and safety.
Lastly, communication is key. Choose a service provider that listens to your needs and provides clear, detailed quotes and timelines. Establishing a good rapport with your welding service can ensure a smoother process and a more successful outcome for your projects.