Vacuum Formers: A Key Tool in Modern Plastic Fabrication
Vacuum forming has become a crucial method in plastic shaping due to its efficiency and versatility.
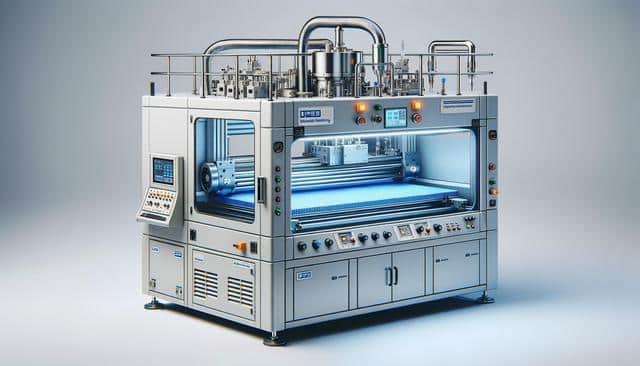
Understanding What a Vacuum Former Is
A vacuum former is a specialized machine used in the thermoforming process to shape plastic materials. It works by heating a plastic sheet until it becomes pliable, then stretching it over a mold and using suction to pull the material tightly against the mold surface. Once it cools, the plastic retains the shape of the mold. This method is widely used in both small-scale and large scale vacuum forming operations due to its simplicity and cost-effectiveness.
There are several types of vacuum formers available, including desktop models for prototyping and industrial machines for high-volume production. A plastic vacuum former can be used to manufacture a variety of items, such as packaging, automotive components, and even custom enclosures for electronics. This adaptability makes it a popular choice across many industries.
Typical features of a vacuum former include:
- Heating elements to soften the plastic sheet
- A vacuum system to remove air between the mold and plastic
- Clamping mechanisms to hold the plastic in place
- Cooling systems to solidify the formed plastic quickly
Applications of Large Scale Vacuum Forming
Large scale vacuum forming is commonly used in industries where mass production of plastic components is required. These include automotive, medical, agricultural, and consumer goods sectors. The process allows manufacturers to produce large, durable, and lightweight parts with consistent quality and minimal material waste.
In automotive manufacturing, large scale vacuum forming is employed to create interior panels, dashboards, and trunk liners. In the medical field, this technology is used to produce equipment housings and sterile packaging. Its ability to create complex shapes with fine detail makes it especially valuable for applications where precision is crucial.
Key advantages of large scale vacuum forming include:
- Lower tooling costs compared to injection molding
- Faster turnaround times for production
- Scalability for different production volumes
- Compatibility with numerous plastic materials
Choosing the Right Plastic Vacuum Former
When selecting a plastic vacuum former, several factors should be considered to ensure it meets your production needs. These include the size of the forming area, the type of heating system, the strength of the vacuum pump, and the overall build quality of the machine. Additionally, it is important to consider the types of plastic you plan to work with, as not all machines are compatible with every material type.
For businesses looking to scale up, investing in a high-capacity plastic suction molding machine can provide long-term benefits. These machines are designed to handle continuous operation and can produce large batches of parts with minimal downtime. They are ideal for manufacturers looking to increase efficiency and output without compromising on quality.
When evaluating options, it helps to look at:
- Machine specifications and capabilities
- Availability of technical support and maintenance
- Energy efficiency and safety features
- Warranty and service agreements
Understanding the Vacuum Former Price Range
The vacuum former price can vary widely based on several factors, including size, features, brand reputation, and intended use. Entry-level machines suited for small-scale or educational purposes are generally more affordable, while industrial-grade plastic suction molding machines can represent a significant investment. However, the cost is often justified by the machine’s capabilities, output speed, and durability.
For businesses or individuals considering purchasing a vacuum former, it is important to conduct a cost-benefit analysis. Determine whether the expected production volume and application justify the investment. Consider not just the initial purchase price, but also the long-term operational costs such as maintenance, energy use, and consumables.
Factors influencing vacuum former price include:
- Machine size and forming area
- Automation features and controls
- Material compatibility and temperature range
- Manufacturer support and spare parts availability
Future Trends in Plastic Suction Molding Technology
As technology advances, the plastic suction molding machine continues to evolve with improvements in automation, precision, and sustainability. Modern vacuum formers now often include digital controls, advanced sensors, and energy-efficient components. These innovations help reduce waste, improve repeatability, and lower the carbon footprint of manufacturing operations.
There is also growing interest in integrating vacuum forming with other technologies, such as CNC machining and 3D printing, to enhance prototyping and production processes. This hybrid approach allows for greater flexibility and customization, enabling manufacturers to respond quickly to changing market demands.
Key developments to watch for include:
- Smart sensors for real-time monitoring
- Eco-friendly materials and recycling systems
- Modular designs for easier upgrades
- AI-driven process optimization
Conclusion
For manufacturers, designers, and entrepreneurs, the vacuum former represents a practical and efficient tool for shaping plastic components. Whether using a plastic vacuum former for low-volume prototyping or a plastic suction molding machine for large-scale production, this technology offers a reliable solution for many fabrication needs. Understanding the range of options, applications, and factors influencing vacuum former price helps ensure a smart and effective investment in your production capabilities.